Table of Contents
In this blog post we focus on the analysis of the biogas. For this purpose, let us again recall the individual gas components that are produced in a biogas plant.
The two main components are methane and carbon dioxide in a percentage ratio of about 50/50. Other components include water vapour, oxygen, nitrogen, ammonia, hydrogen and hydrogen sulphide. Methane is the most important component because, as already mentioned in the previous blog post on biogas, methane is the component with the greatest benefit for energy production. Methane burns with oxygen and is converted into carbon dioxide and water with low emissions.
In order to obtain the best possible quality of the raw biogas, the concentrations of the undesirable components of the biogas can be reduced by taking appropriate measures. The factors that have a negative effect on the biogas and the measures that can be taken to counteract them are described in the next paragraph.
Which factors do have a negative effect on the quality of the biogas?
1. Humidity
Humidity is basically not the big problem. Rather, the harmful substances in the moisture can lead to valve, bearing and line damage in the area of the engine during gas utilisation. The following harmful ingredients were found in test results:
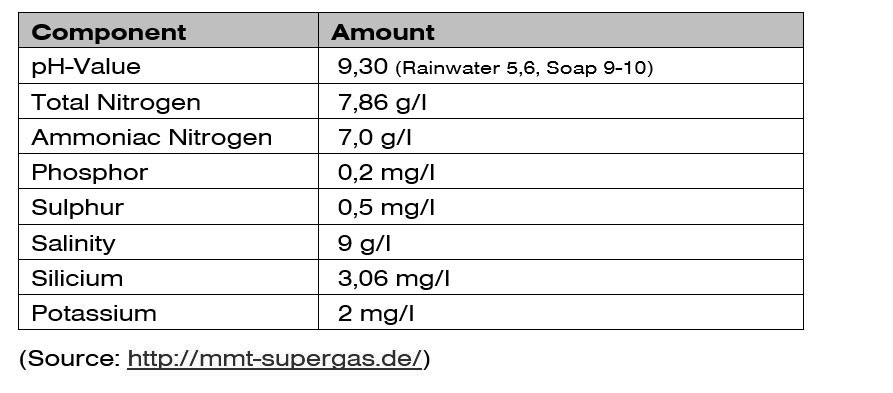
The values given are examples measured at a biogas plant and may vary from plant to plant. The values given are examples measured at a biogas plant and may vary from plant to plant.
The amount of humidity contained in the biogas depends on the gas temperature. In the fermenter, the biogas is saturated with water vapour. If the temperature of the biogas is lowered, part of the water vapour condenses accordingly and can thus be separated from the gas flow. The dehumidification of the biogas can be realised with the help of electric cooling units or buried gas pipes.
2. Hydrogen sulphide
Hydrogen sulphide is produced by the degradation of protein-rich compounds in the substrate. The concentration of this gas is usually in the range of 0 – 1500 ppm (10,000 ppm corresponds to 1 vol.%). On the one hand, this aggressive compound leads to the corrosion of plant components. On the other hand, combustion in the CHP produces sulphur dioxide, which in turn leads to corrosion of the fittings and the engine. Most manufacturers of CHP units and boilers set limits for hydrogen sulphide that must not be exceeded in order to avoid corrosion damage.
As a general rule, biogas should be desulphurised to keep the concentration as low as possible.
How can you reduce hydrogen sulphide in biogas?
Option 1 - Oxygen supply
By adding oxygen to the substrate, it is possible to convert hydrogen sulphide to elemental sulphur and thus reduce the concentration. This method is common practice at agricultural biogas plants. Regular monitoring is important with this method. This means that a sufficient oxygen supply should also be ensured at the end of the flow section so that the increase in concentration due to sulphide formation there is prevented. However, the oxygen content should not be too high either, as this can lead to corrosion of plant components and the methane-producing bacteria work better in the absence of oxygen.
Option 2 - Ferrous sulphate
The addition of iron sulphate results in a binding of the hydrogen sulphide, which in return leads to a lowering of the concentration. The basis of H₂S binding by means of iron salts is the high affinity of iron towards sulphides. Regardless of the binding or valence form in which the iron is present, the formation of iron sulphide (FeS) always occurs in the presence of sulphides. Due to the low solubility of FeS, competitive reactions with other water constituents can be excluded.
Option 3 - Activated carbon filter
The biogas is passed through a special activated carbon. The predominant components methane and carbon dioxide pass through the activated carbon. The hydrogen sulphide is converted into sulphur and hydrogen by the activated carbon through a chemical reaction and thus does not cause any damage to the engine and thus ensures the lowest possible failure rate. How long the activated carbon is able to convert the hydrogen sulphide depends on the concentration of H₂S and the biogas volume flow.
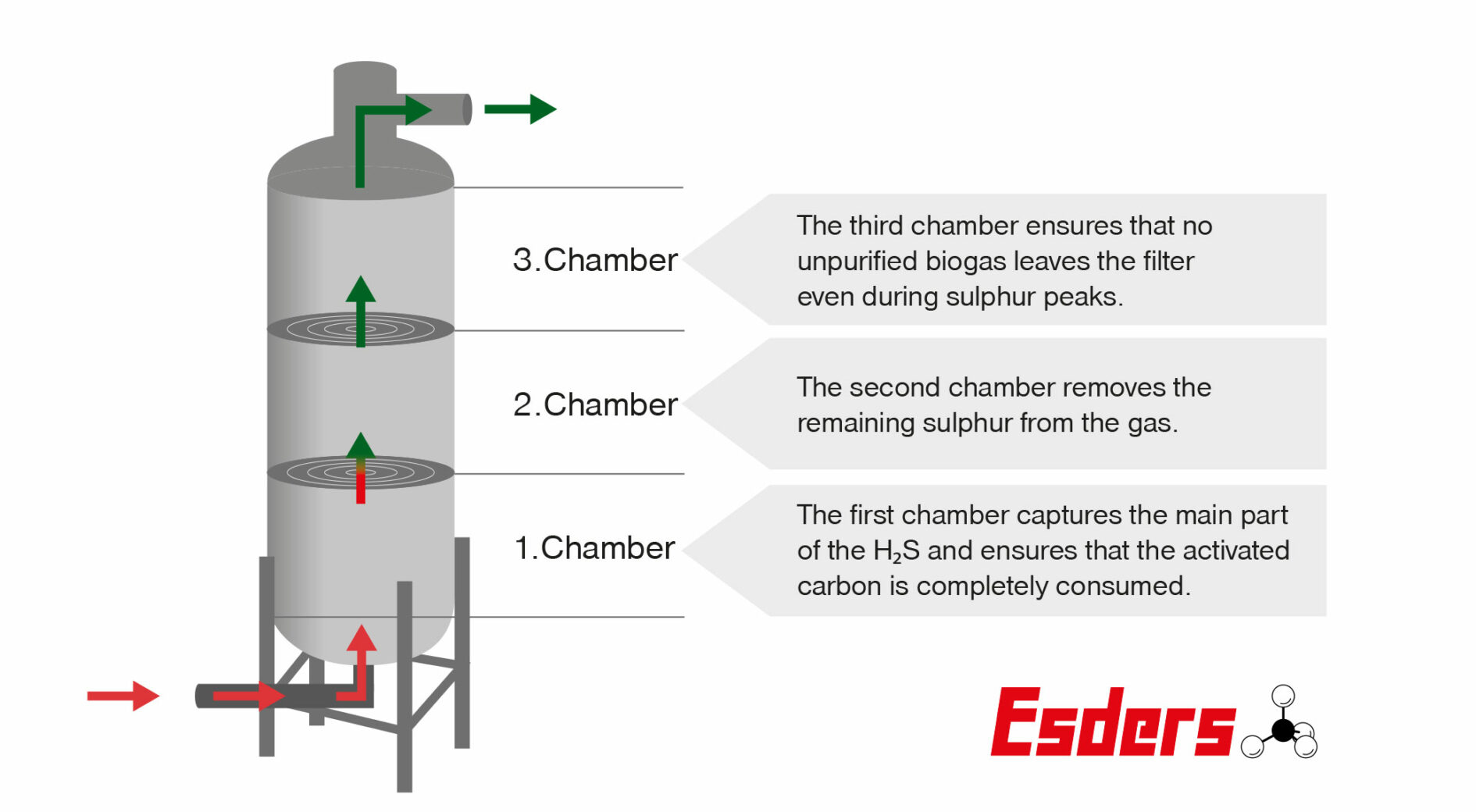
Measuring
State-of-the-art infrared technology can be used to measure very low concentrations (ppm range) down to 100 vol.% methane and CO₂. The electrochemical sensors for oxygen and hydrogen sulphide also allow these concentrations to be determined.
The following measuring ranges are covered:
Methane: 0-100 vol.% CH4
Carbon dioxide: 0-100 vol.-% CO₂
Oxygen: 0-25 vol.% O₂ (optional)
Hydrogen sulphide: 0-2,000 ppm H₂S (optional)
After selecting the menu item for biogas measurement, the sensor adjustment phase begins. It only lasts about 25 seconds and should always take place in fresh ambient air. After the sensor settling phase, the unit displays the current measured values. These should be “0” in fresh air (exception O₂ and CO₂). In order to obtain exact results during measurement, flawless tubes and adapters are used. Gas-tight connections from the measuring point to the measuring device prevent ambient air from falsifying the measurement results. A mobile gas measuring device for analysing biogas gives you the opportunity to carry out measurements at several points in the biogas plant. Precise measurements at selected measuring points make it easier to assess measures for optimising the plant.
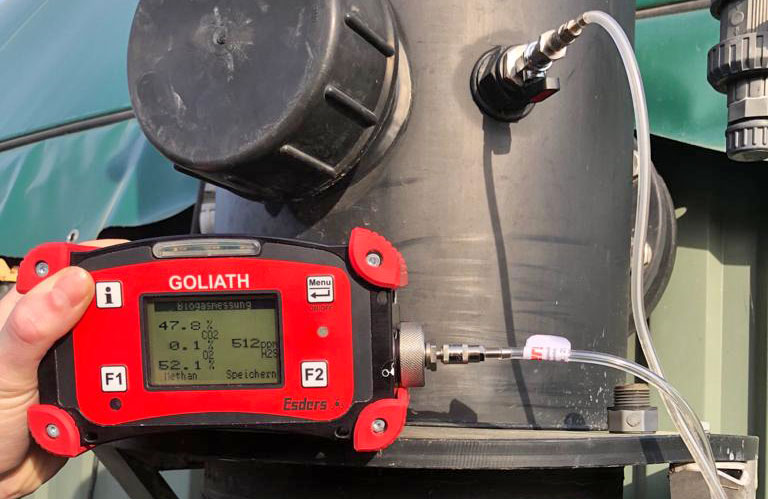
We select different measuring points. We carry out the first measurement with our GOLIATH at the overpressure and underpressure protection of the fermenter.
We carry out another measurement before and after the activated carbon filter. It is useful to keep an eye on the saturation of the activated carbon.
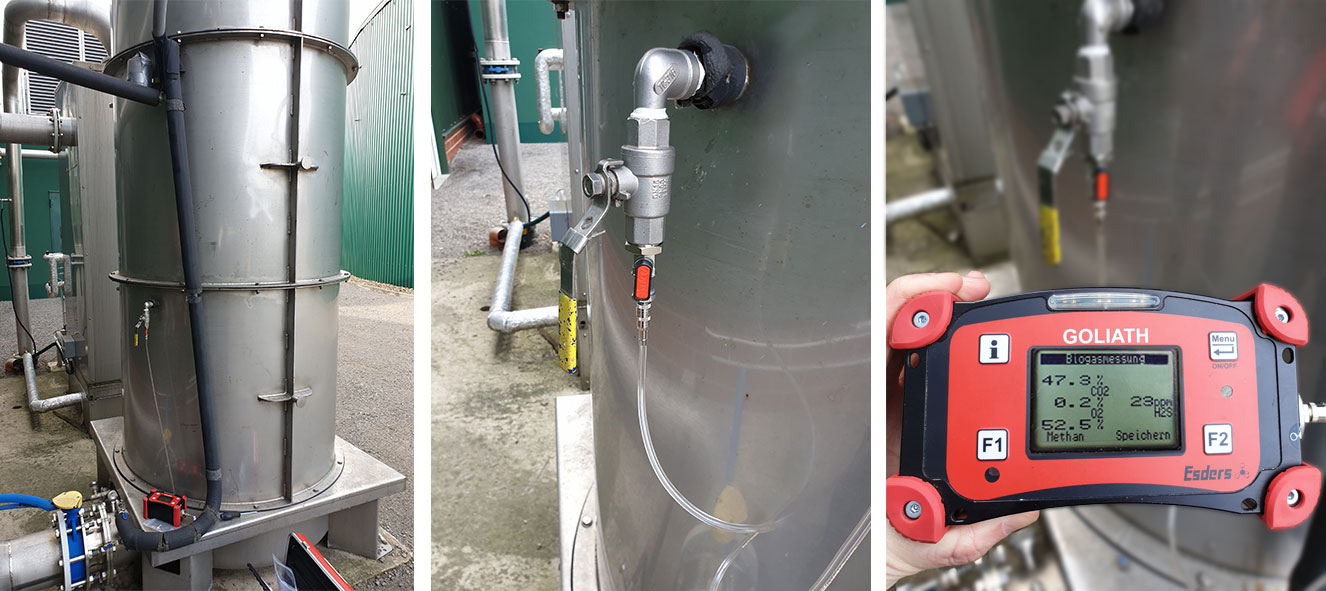
In another blog post on biogas, we look at leak detection on biogas plants and show different methods in this context, including remote detection with a GasCam.