Table of Contents
After recording the leaks and defects as described in our second blog post on industrial gas, we now move on to their removal and documentation.
We would like to start this blog with a key topic that is part of every inspection of an industrial gas facility. After all, it is not only a matter of recording defects, but also of having them professionally rectified within a specified time frame. We already referred to these points in the last blog on leakages and defects.
Corrective measures of defects
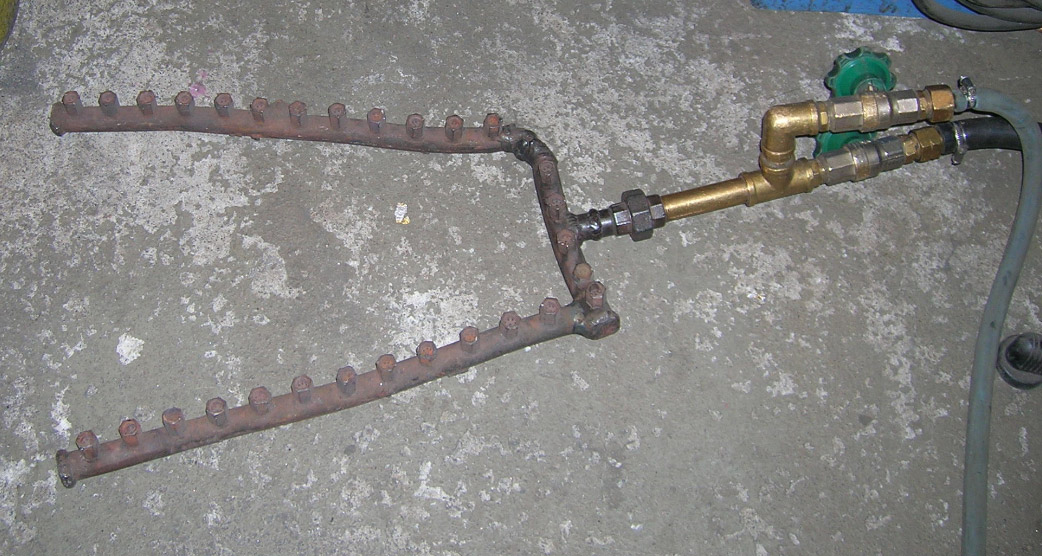
Only specialists from contracted installation companies may be commissioned with the elimination of identified defects such as leaks and damage to fittings. They should have participated in relevant further trainings.
Of course, pipeline construction companies according to the German GW 301 may also be commissioned with the repair work on pipeline-like pipeline systems, as they are often found in an industrial gas supply system, and they are usually better equipped for such work.
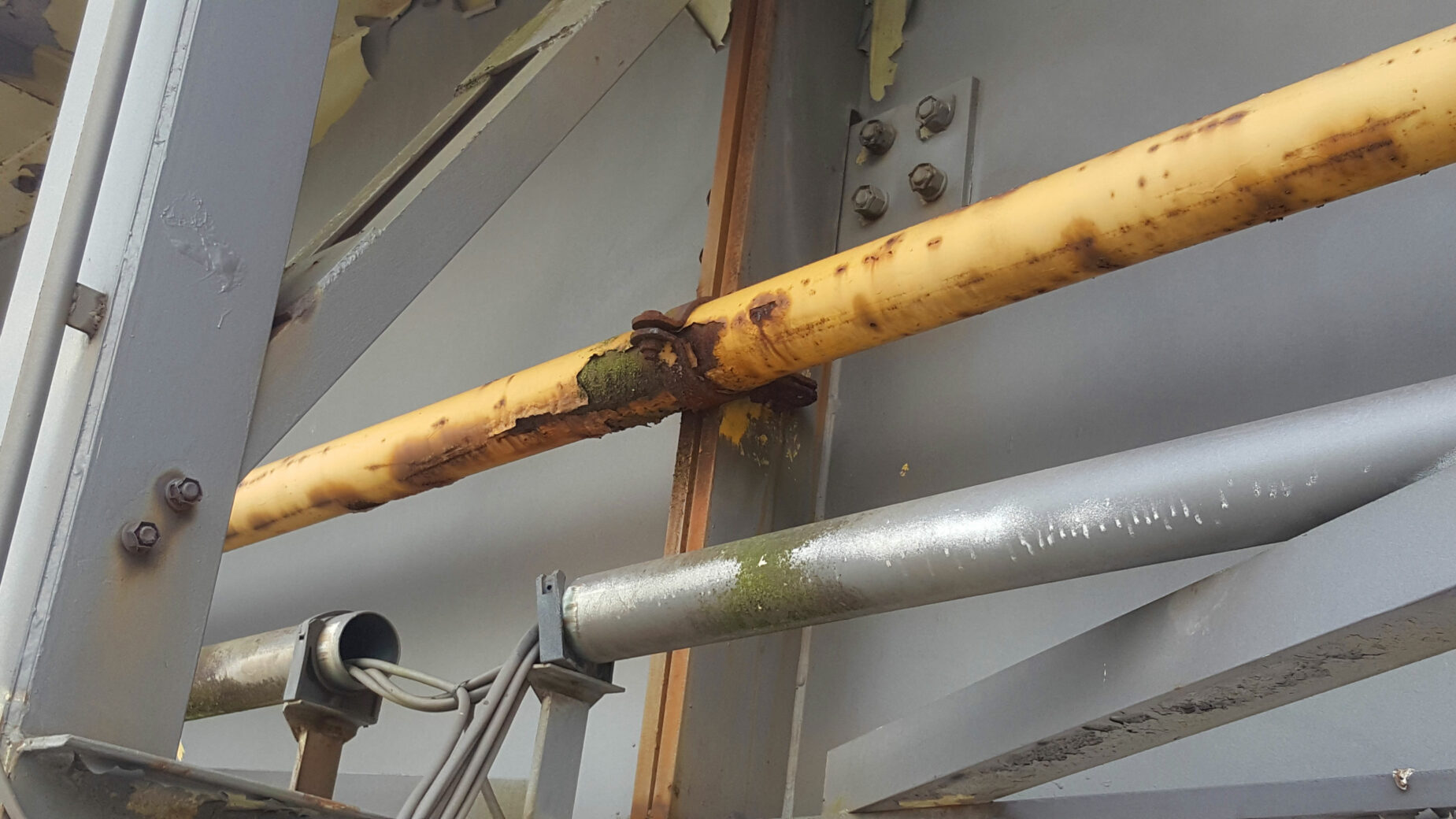
External maintenance work, such as the application of flow direction markings, corrosion protection measures and yellow protective paint, can be carried out by in-house personnel.
Maintenance and repair
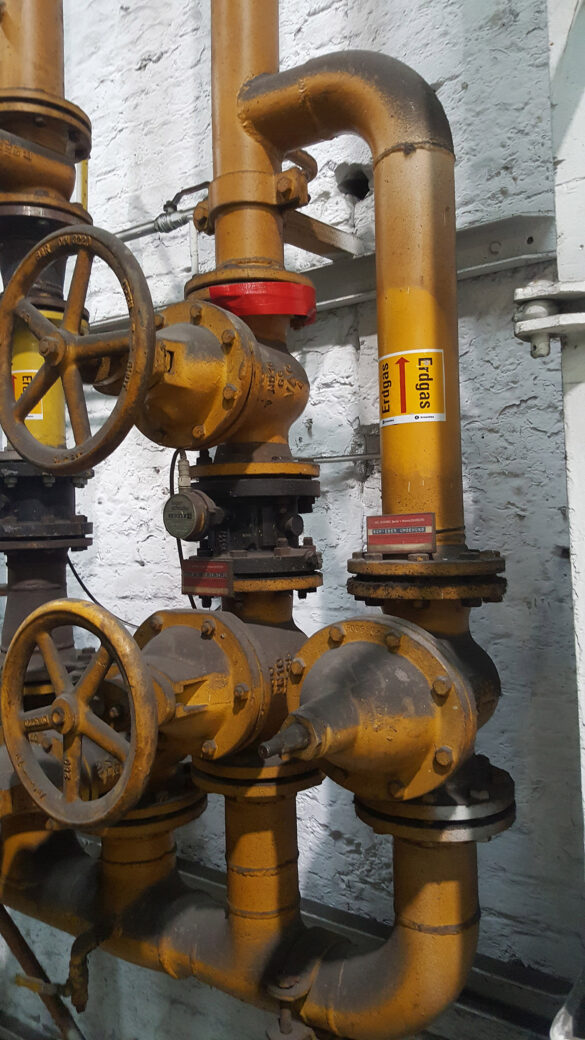
A maintenance strategy that is optimally tailored to the respective plant operation and condition helps to save costs while ensuring availability and operational safety. With the application of condition-based maintenance, safety and reliability as well as the availability of a gas plant are guaranteed, with the highest possible utilisation potentials being exploited.
The operator is responsible for the maintenance of the gas installation. This must be carried out and documented in accordance with the German DVGW Codes of Practice G 495, G 600, G 465-1 and G 466-1.
The repair work must be carried out on the basis of DGUV 100, DVGW worksheets G 600 (TRGI) and G 614-2.
The work presented in the blog series “Industrial Gas” only covers the pipeline system and its components up to this point. In order for the operator to fully comply with his duty to ensure operational safety, he should also be informed about the topic of organisational structures and the required documentation obligation.
Organisational structure of the plant operator
A review of the organisational structure of the plant operator is normally not the subject of an assessment of a pipeline system with its components. For this reason, it is recommended that the contractor informs the client that he is responsible for comparing his internal organisational structure with the requirements of the German DVGW (A) G 1010 “Requirements for the Qualification and Organisation of Operators of Natural Gas Systems on Plant Premises” and, if necessary, adapting it accordingly.
Documentation of the operator
Documentation should be available for the gas installation in accordance with DIN 2425 and DVGW note GW 120 and should contain the following documents:
- Information on the dimensioning of the gas pipelines
- e. g. pressure, nominal width, pipe material and flow rate, static proofs
- Proof of qualification of the executing company and the welders used
- Detailed drawings and as-built plans (DIN 2429-2) including special structures
- Proof of the quality characteristics of the installed pipes and pipeline components (e.g. pipe book according to DVGW (A) G 462, DVGW (A) G 463)
- Pipe logbook on the welding work and pipe laying in the course of the construction progress
- Certificate of the manufacturer and the installer
- Test records
- e. g., non-destructive material test, diagrams and evaluation of the pressure test
- on the functional test of the gas pressure regulators
- on recurring tests
- Acceptance certificate
- Location of the piping system
- Floor plan drawing with pipe routing
- Locations and dimensions of shut-off valves for test purging and venting equipment.
- Locations and construction of internal gas pressure control systems with details of the required settings for control devices and safety devices
- Locations of metering equipment
- connected gas utilisation facilities
- Operating instructions
The operator’s internal documentation must be checked for completeness according to the above list and amended if necessary.
Gas pressure control
The operator is required to apply the deadlines for maintenance and functional checks at his own responsibility, taking into account the individual loads on the gas installation and the available operating experience.
The introductory remarks must be taken into account in particular when operating gas pressure regulators for which the owner of the gas installation is responsible. For gas pressure regulators with inlet pressures up to 100 hPa, maintenance and functional checks must be carried out as required. For operating pressures above 100 hPa up to 0.1 MPa, a 12-year functional test of the regulator and the safety devices is mandatory.
These maintenance measures of the components and assemblies can be carried out by the operator himself, if he has the necessary qualifications, or by specialist companies.
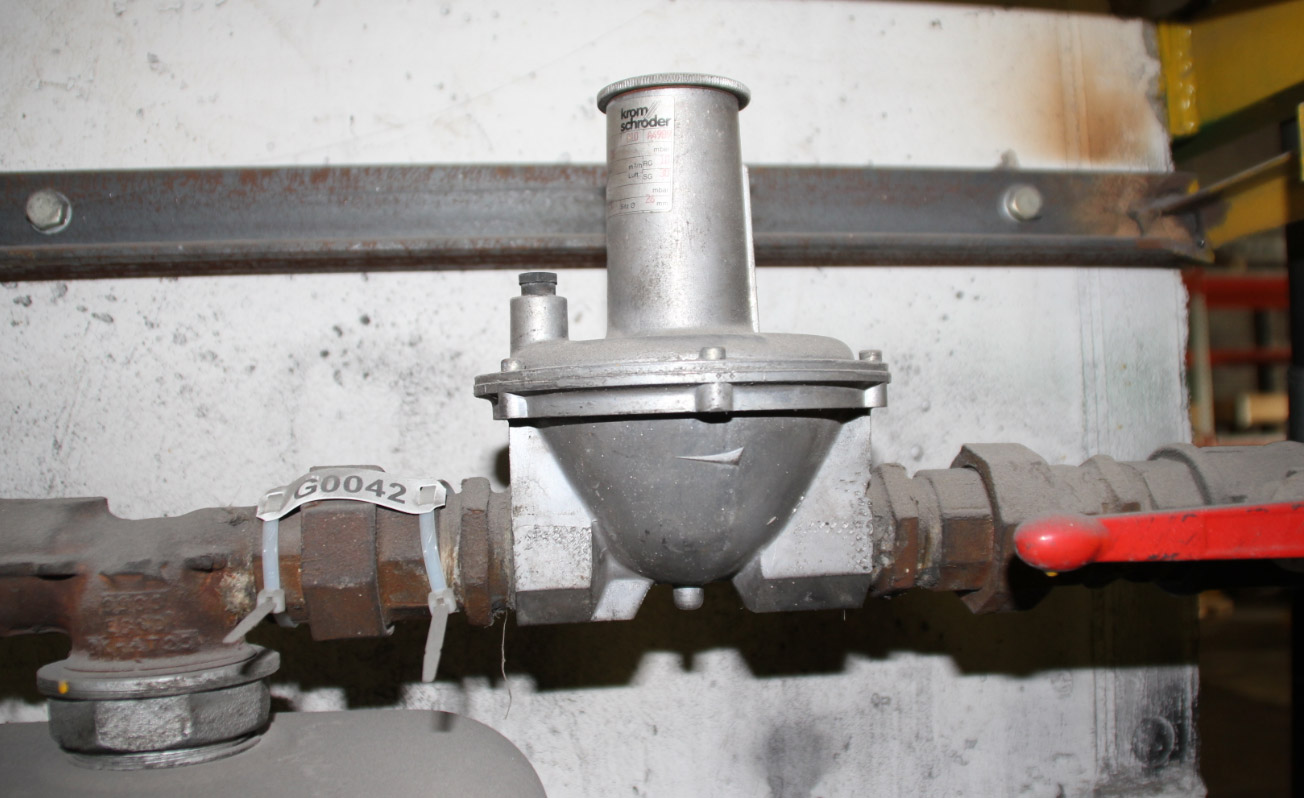
Future inspection intervals
To conclude this blog, I would like to address the important issue of future inspection periods. For gas pipeline systems with regard to tightness, corrosion protection and functional efficiency, these are normally to be determined according to the operating conditions by the operator, who, however, often does not have the necessary operating experience. Thus, they are dependent on the input and recommendation of experts. The first periodic inspection should be carried out at the latest 6 years after completion and thereafter at shorter intervals. The German DVGW (A) G 465-1 and DVGW (A) G 614-2 guidelines, for example, would also provide assistance here.
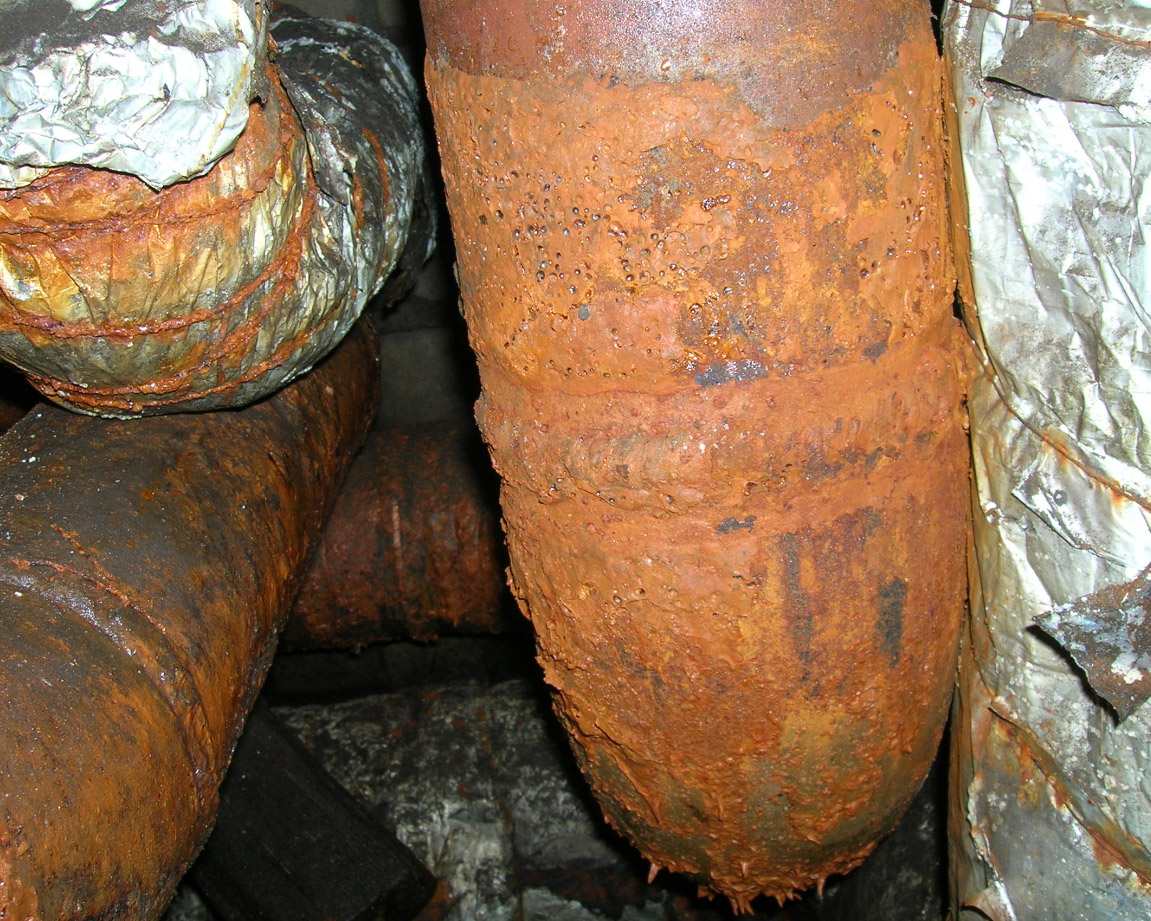
The intervals for regular, recurring inspections for leaks naturally depend on the operating conditions, the technical condition of the gas pipes and the frequency of leaks in relation to the length of the pipe. The minimum inspection period for gas pipelines with operating pressures < 1 bar is determined according to the leakage frequency per 100 m pipeline length and is based on the specifications of DVGW (A) G 614-2:
- Leakage <= 0.1/100 m: period of the next inspection 6 years
- Leakage <= 0.5/100 m: period of the next inspection 4 years
- Leakage <= 1/100 m: period of the next inspection 2 years
- Leakage > 1/100 m: Period of the next inspection 1 year
Exposed gas pipelines can be divided into test sections and subdivided and separated according to the operational conditions.
In order to be able to apply this recommendation, it is imperative to have a site plan with the pipe system drawn in to define test sections. If this subdivision is not made, the entire pipe network would be included in the consideration and the inspection interval for the entire network could be shortened if a larger number of leaks were detected in one area. The classification and allocation can be made individually by the expert according to his or her personal experience. However, it should be comprehensible for everyone. For example, buried outdoor pipelines can be combined into one test section, and individual halls or operating facilities also offer the possibility. A subdivision into pressure stages would also be a variant.
Example: Site plan with pipeline system, test sections and defect numbering
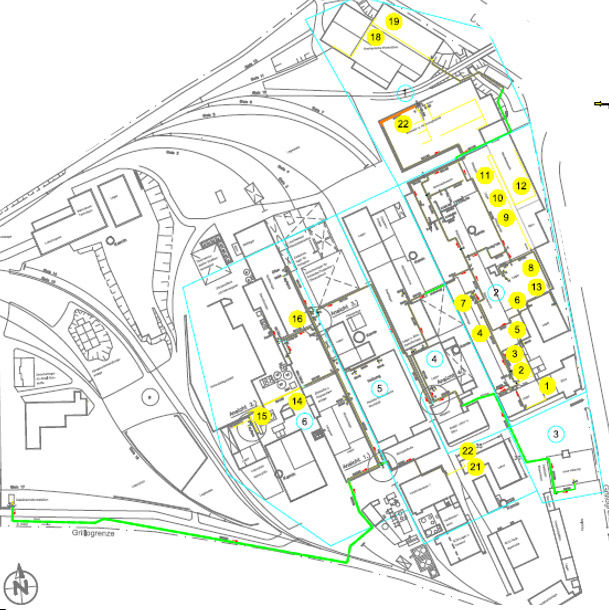
Example table (not identical with site plan):
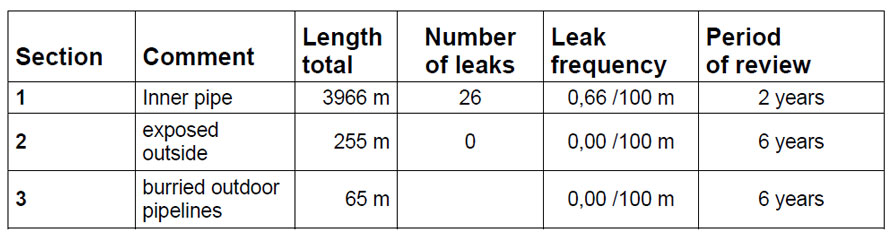
A correction factor could be used for gas pipelines not shown in the pipeline plan. This must also be technically justified and recorded in writing.
For buried outdoor pipelines, a period of 4 years usually applies for a recurring inspection.
Measurement technology
For the inspection of buried outdoor pipelines, a gas detector with a short T 90 reading time and a highly sensitive sensor (CH₄) is suitable for systematic pipe network inspection, such as the HUNTER.
A mobile laser measuring device, such as the new ELLI, is suitable for leak testing and checking exposed pipelines in gas systems, with which methane can be reliably detected from a distance.
About the author of our blog series Industrial Gas:
We would like to thank our guest author Mr. Holger Schröder for sharing his expertise with us and would like to take this opportunity to briefly introduce him.
Holger Schröder has been working in the gas and water sector for more than 40 years. The state-certified technician in the field of sanitation, heating and air conditioning was most recently employed as head of the meter service department at Netze Duisburg GmbH.
He can look back on decades of involvement in various DVGW committees and, as a TRGI expert, has also been inspecting gas installations on company premises with his staff since 2001. As the chairman of the Technical Committee Gas Installation, he appeared as co-author of the commentary on the DVGW-TRGI 2018.
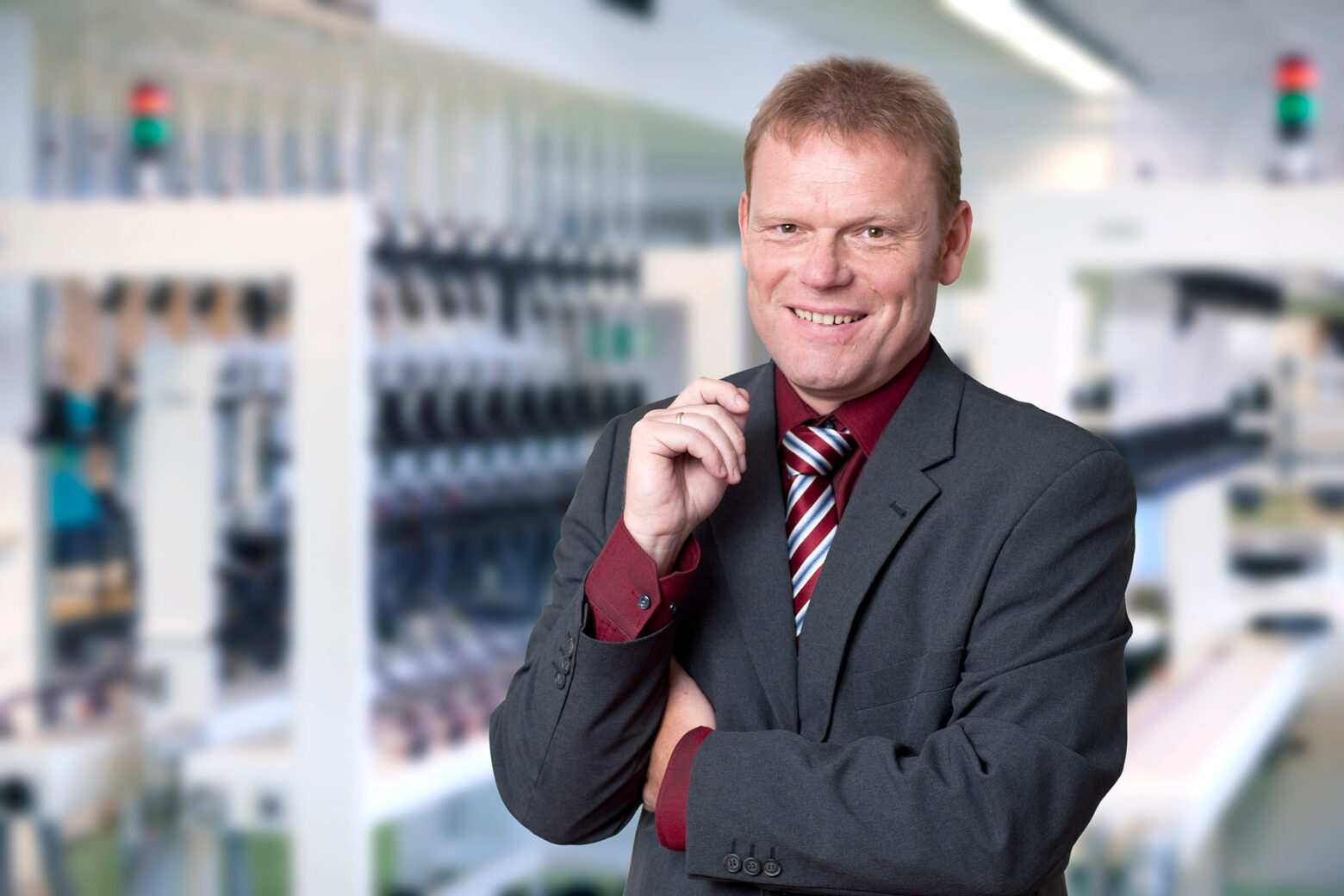