Table of Contents
Our guest author, Holger Schröder, is an absolute expert in this field, he is a TRGI expert and co-author of the TRGI 2018 commentary.
Industrial gas companies generally distribute electricity, natural gas and drinking water on their own responsibility via their pipeline systems on their premises. The connecting customer or, more precisely, the company management is responsible for the proper condition of this technical system. The responsibility usually starts behind the gas measuring and regulating system and ends behind the exhaust gas routing.
A gas installation constructed in accordance with the statutory regulations and the relevant codes of practice of the German Technical and Scientific Association for Gas and Water (DVGW) provides the prerequisite for proper operation of the gas installation in the long term.
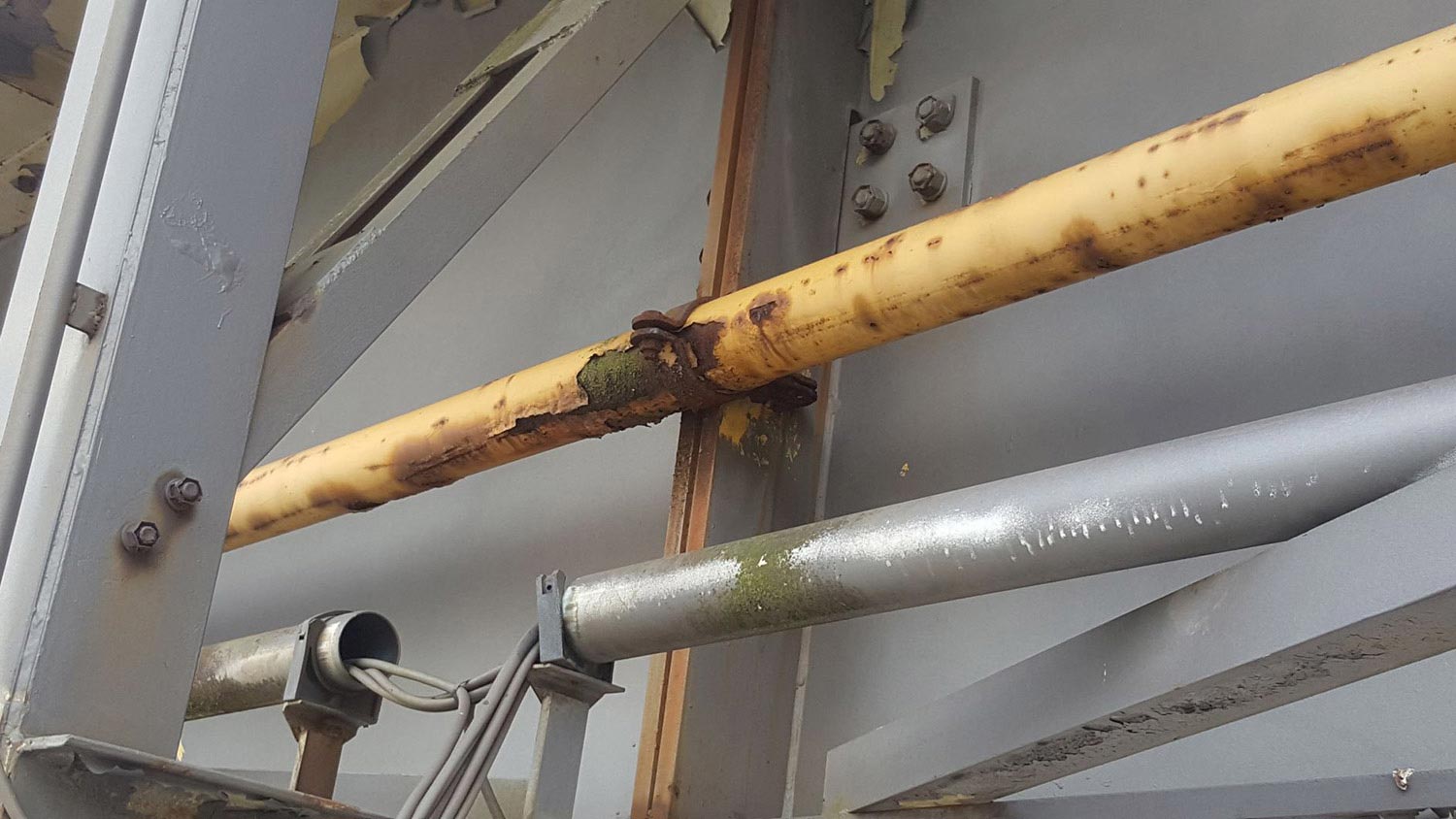
During operation, changing conditions such as weather influences, corrosive ambient air or mechanical damage can have an effect on safety. To ensure proper functioning and maintenance of the safe operating condition, the relevant operating instructions and information provided by the component and device manufacturers must be taken into account. The DVGW also recommends regularly recurring control and inspection measures at fixed time intervals with concluding written documentation.
As a network operator, you are well advised to inform your industrial customers extensively about this topic. Information sessions of about 90 minutes have proven to be useful. Based on this, individual personal discussions about the necessity of a comprehensive plant inspection should be held with the company management and the technically responsible persons.
Gas plant
The natural gas supply of the company featured in this blog was from the medium pressure network of the local network operator. In the company’s own gas measurement and regulating system, the operating pressure was reduced to
100 hPa (mbar).
The pipeline network consisted of buried and exposed outdoor pipelines as well as exposed indoor pipelines.
Thus, an extensive variety of materials was to be expected during the inspection. The area of gas use consisted of ceiling radiators, boilers and burners for preheating materials, which are common for industrial plants.
The scope of testing described here only covers the pipeline system and its components up to and including the equipment shut-off device.
According to the operator, the gas appliance connection lines and the general condition of the gas appliance were inspected by specialist companies as part of the gas appliance maintenance.
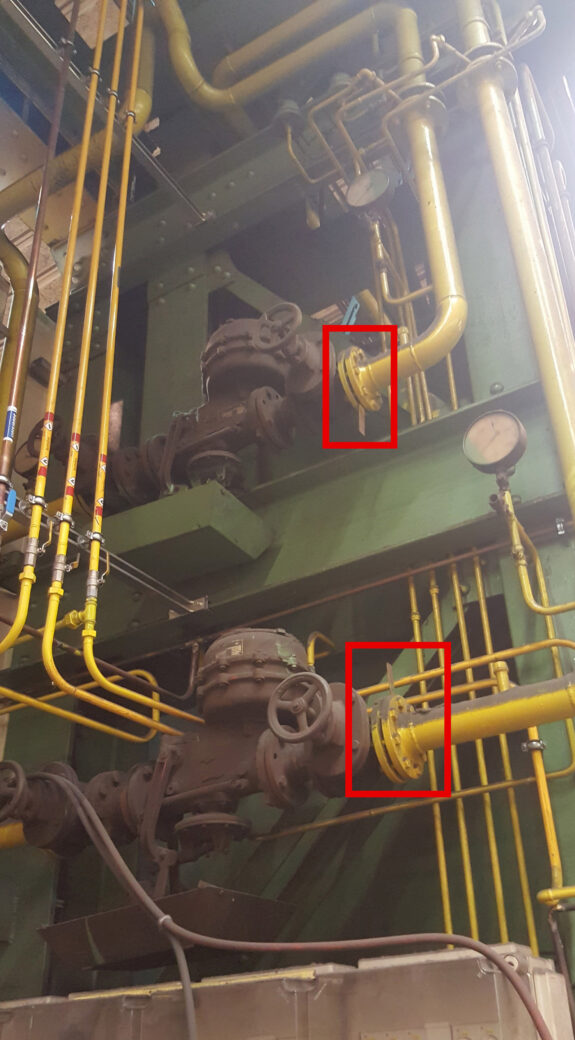
Methods and measuring devices for leak testing
The assessment of the accessible exposed gas pipeline for leaks was carried out using the gas detector LeckOmiO EX. This device detected the smallest gas concentrations via a highly sensitive hand-held sensor and naturally fulfilled the requirements of DVGW (H) G 465-4 Gas detection and gas concentration measuring devices for the inspection of gas systems.
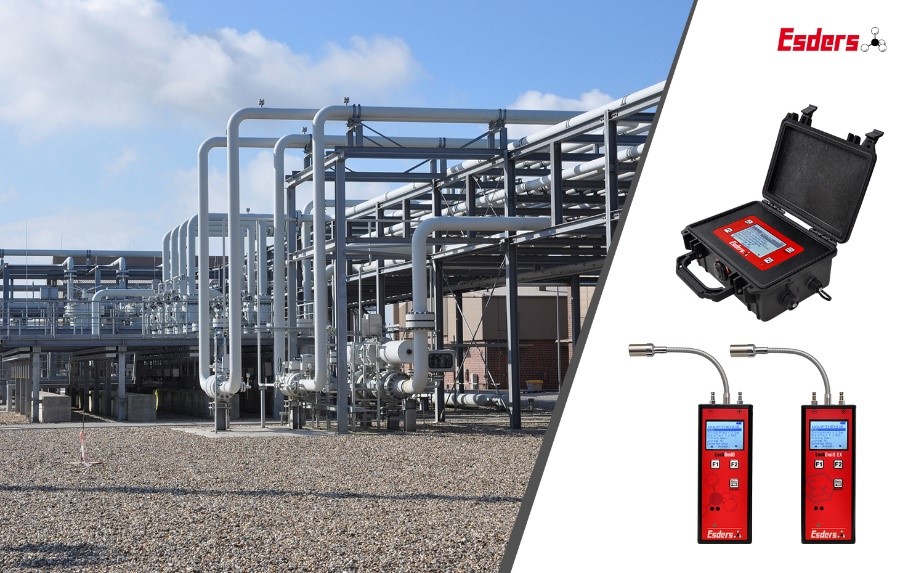
For operational reasons, an underground pipeline had to be tested for leaks by means of pressure measurement. For this purpose, parts of the plant could be temporarily taken out of operation by means of shut-off valves. The smart memo pressure measurement case was connected to a measurement opening and recorded the pressure curve over a period of several hours. The test pressure was about 5% below the actual operating pressure. This made it possible to test the shut-off gate valves for internal leakage at the same time. Finally, the diagram was evaluated.
Saving time in everyday work - What possibilities does the latest technology offer for inspecting gas plants?
In addition to the standard procedure, there are other possibilities for an overall assessment. These can support the proven methods and the work with hand-held measuring devices, but they cannot replace them.
Outdoor drone use
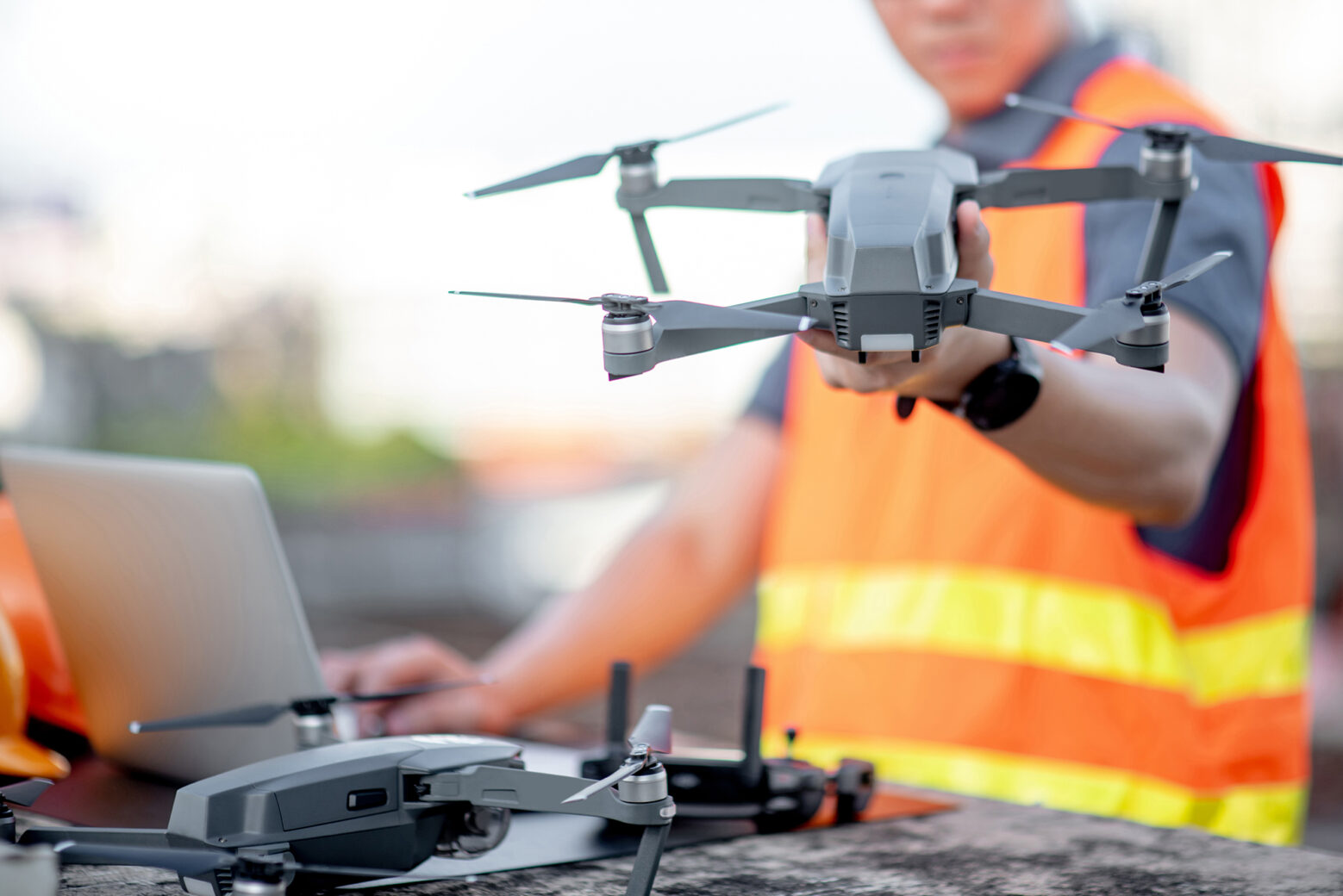
Inspecting a large industrial plant with a hand-held meter takes a lot of time. Not all parts of the pipeline are freely accessible and many kilometres of gas pipeline have to be examined. Exposed outdoor pipelines that may have weather-related damage can be located in a first step with the help of a drone and a camera. The inspector on site can give precise instructions to a trained specialist – who flies the drone – as to which positions must be approached and, via a transmission on the display, assess which parts of the gas pipes are to be checked for leaks in a second step with a hand-held measuring device. With this procedure, many kilometres of external pipelines can be checked and inspected in a shorter time. The inspector can thus get a quicker overview of the overall condition of the system.
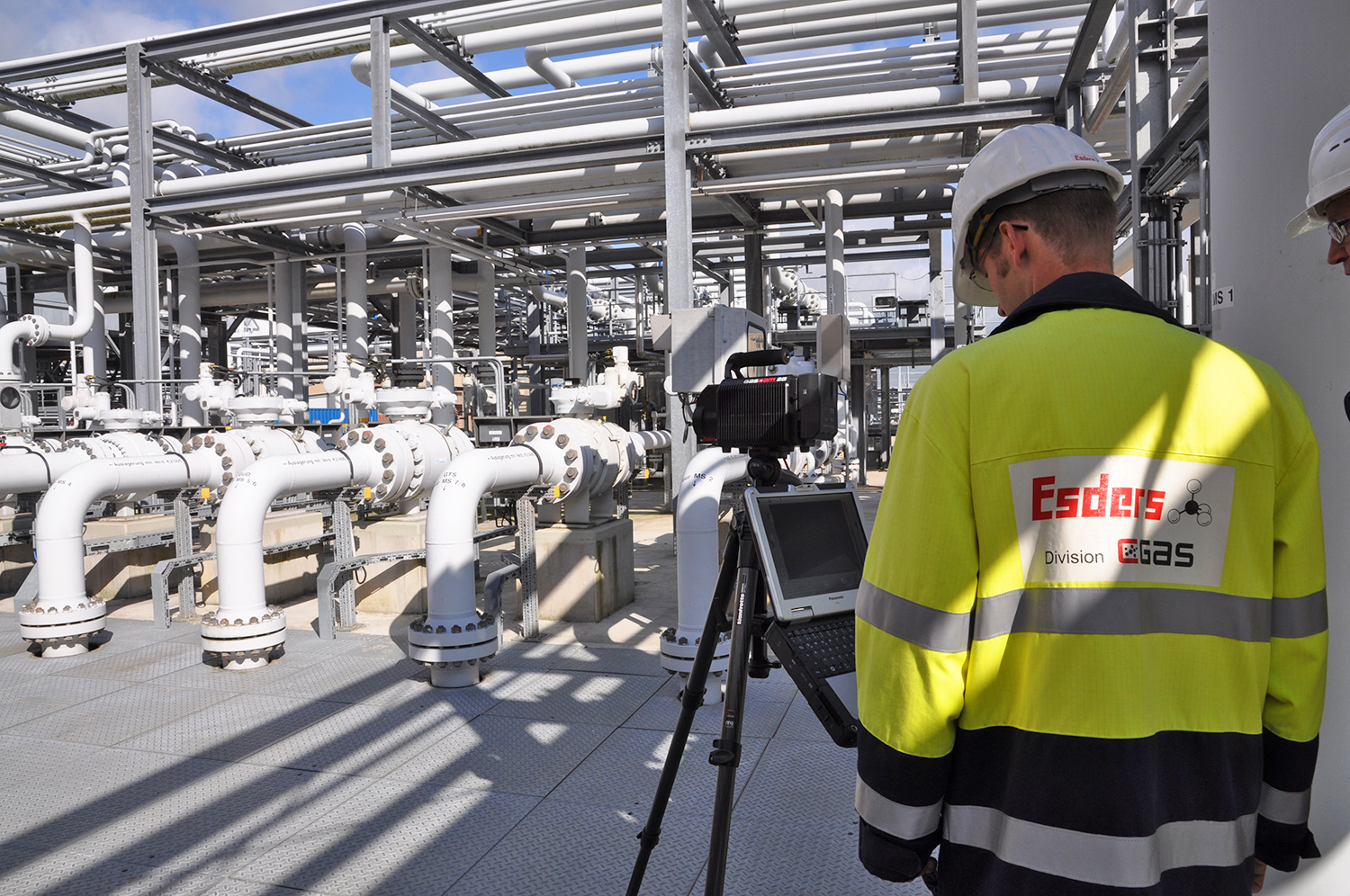
Remote gas detection outdoors
Another option for checking gas pipelines outdoors is offered by the latest technology in remote gas detection, such as the GasCam. As a highly specialised system for the detection of methane, it has been developed for the leak testing of biogas and natural gas plants. The GasCam is an innovative development in the field of passive remote gas detection using infrared spectrometry. The passive infrared method makes it possible to visualise gas dispersions against an unreferenced background, such as the sky. Even from distances of up to 100 m, methane is reliably detected and displayed as a coloured gas cloud in front of the background in real time.
GasCam use in industry
Indoor active laser infrared spectrometry
For the use of this technique, it is necessary that the laser beam can be reflected. To do this, it only needs to be directed at the spot to be checked. Detailed information on this topic can also be found in our blog post Remote gas detection – laser infrared spectrometry.
A mobile laser measuring device that can be used to conveniently monitor areas that are difficult or impossible to access and hazardous areas from a distance is the ELLI.
Measuring principle ELLI
In a second blog post in our series on the topic of industrial gas, we use concrete examples from practice to go into detail about the damage points that may occur, their recording, documentation and the resulting measures.