In addition to the qualification requirements for personnel and organisational requirements for troubleshooting control, which we have described in a blog post, it is also necessary to fulfil the technical requirements. Thus, in addition to vehicles equipped with the appropriate means of communication, tools and shut-off accessories, certain equipment technology is required in particular. Here we use the term “equipment technology” to refer to the gas measurement technology required for each specific case.
What this means in concrete terms, especially against the background of an increasingly widespread admixture of hydrogen to natural gas, we want to illustrate using the example of our gas warning and gas detection device OLLI.
Indicator test
Shortly after being instructed by the information service and before arriving at the trouble scene, the fault service should take the appropriate gas measuring equipment and check the proper functioning of the gas warning device by means of a short indicator test. This involves visually checking the device for damage and briefly exposing it to a suitable test gas to check whether the device is responding correctly. The integrated pump is also tested for function. With the OLLI, both can be carried out via the so-called “Bump Test”, which can be started from the main menu. We have already created a tutorial on the subject.
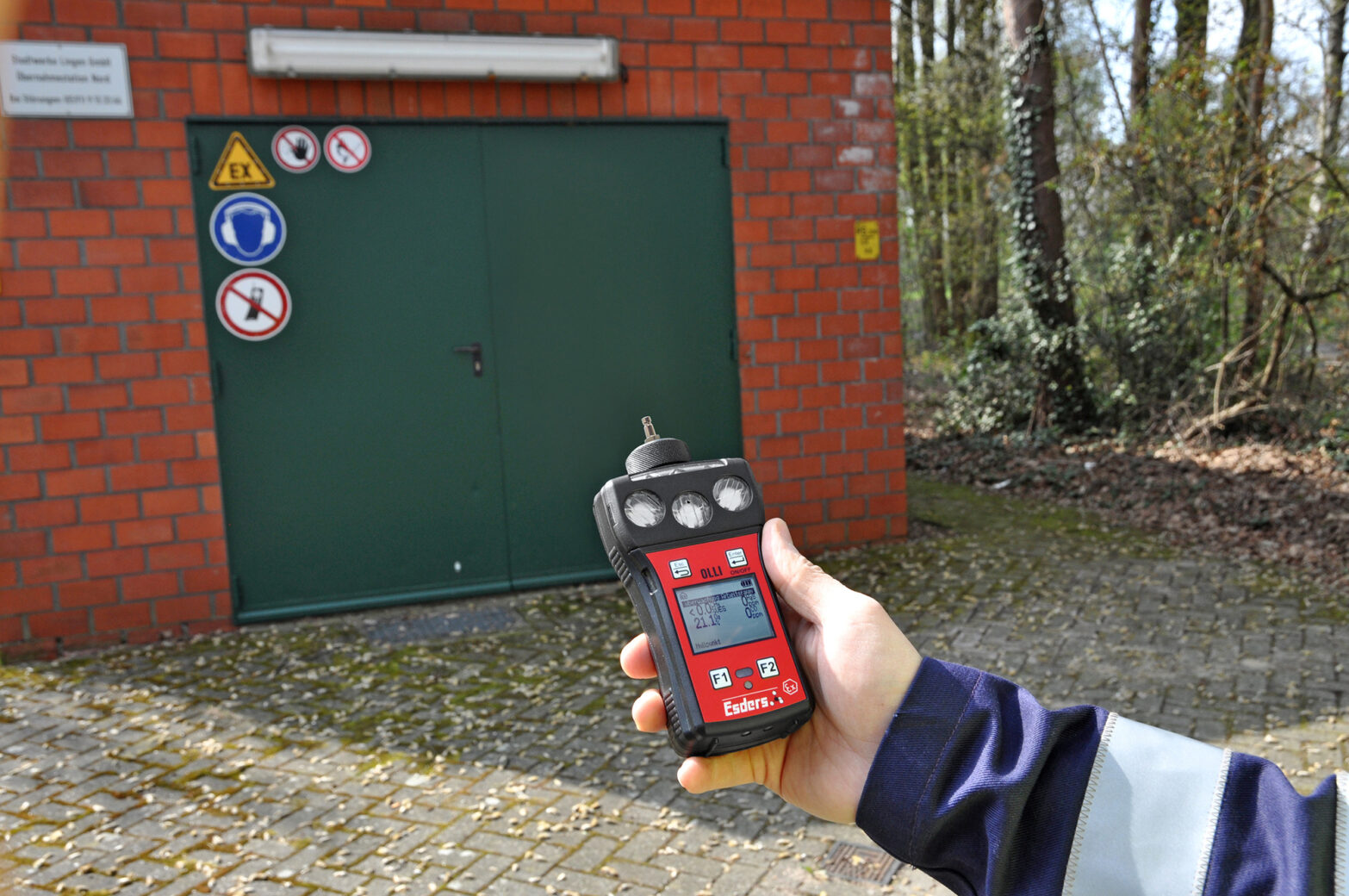
Clearance measurement
On arrival at the site of the fault, the first thing to do is to carry out a so-called “clearance measurement”, i.e. to check with a suitable gas warning device whether an explosive atmosphere is present. For this purpose, a measuring device with a certified explosion protection measuring function according to DIN EN 60079-29-1 should preferably be selected. The OLLI is certified according to this standard, among others. Use the menu item “Confined space entry” for the “clearance measurement” procedure with OLLI. This can already be started on the way to the fault location – after the previously mentioned indication test has been successfully carried out – as the sensors need some time to “run in”. This can save valuable time. It is important to start the device in fresh air so that the zero points of the sensors are set correctly and the measured values are not subsequently distorted. If fresh air (clean ambient air) cannot be guaranteed in the vehicle of the fault clearance service, the running-in phase should only take place upon arrival at the site. When free-measuring with the OLLI, make sure that the gas inlet on the upper side of the device is free of dirt particles or similar impairments and that the gas can flow through unhindered. Furthermore, depending on the conditions on site, measurements should be taken at head height or above, as natural gas is lighter than air and therefore accumulates at the top (e.g. below the ceiling). For the free measurement with an OLLI in the example configuration shown below, it does not matter whether the gas is natural or a mixture of hydrogen (H2) and natural gas with a share of 20 vol.-% H2.
Measuring device and options
Probes
Charging & carrying equipment
Test gases and accessories
Adding H2 to natural gas
By using the measuring principle of heat tinting (catalytic combustion) in the sensor array, both potentially explosive natural gas-air mixtures and hydrogen-natural gas-air mixtures can be reliably measured in the menu item “Monitoring workspace” until the lower explosion limit (LEL) is approached. The sensor behaves almost identically in both cases. No separate calibration of the gas detector is required. This is a highly topical issue for many utilities, as information about the measures of admixing up to 20 vol.-% hydrogen, which are being pushed for ecological reasons, is now made available to a broad section of the population via the German mass media. After thorough internal testing, we, as a manufacturer, can recommend the OLLI as a safe device for measurements, even with a hydrogen impurity of 30 vol.%. Measuring devices that use an infrared sensor to monitor the environment for explosive atmospheres have clear disadvantages here, as an infrared sensor cannot detect hydrogen. However, there are some points to consider when using the OLLI in the above configuration:
- The addition of hydrogen to natural gas reduces the LEL slightly, since hydrogen has a LEL of 4 Vol.-%, but methane (the main component of natural gas) has a LEL of 4.4 Vol.-%. In order to ensure a timely warning of a potentially explosive atmosphere by the gas warning device, a reduction of the alarm thresholds by approx. 5% LEL, possibly 10% LEL, is therefore recommended.
- The electrochemical sensor for the detection of carbon monoxide (CO) is cross-sensitive to hydrogen, i.e. even a very small amount of 100 ppm (= 0.01 vol.%) hydrogen in the atmosphere can, under certain circumstances, lead to a reading of up to 30 ppm CO
The smell of natural gas does not change when up to 30% vol. of hydrogen is added, i.e. the characteristic smell of gas can be detected even at very low concentrations of around 200 ppm.
Locating the leak
If the accident location has been “safe”, i.e. if it has been ensured by means of a gas warning device that there is no potentially explosive atmosphere and thus no immediate danger, the origin of the gas leakage is usually determined. For this purpose, the menu item “Building inspection” is used in the OLLI, which reacts sensitively to very low concentrations (ppm range), especially in the lower measuring range. Before changing from “Confined space entry” to “Building inspection”, it is again important to let the sensor run in fresh air so that the zero point is set correctly. If the change is mistakenly made directly in a room contaminated with gas, the actual gas concentration may subsequently be incorrectly estimated. To avoid this, it is sufficient, for example, to position the measuring device at the open basement window during the run-in phase of the “Building Inspection”. Afterwards, the origin of the gas leak can be determined with the OLLI and the attached hand probe by “walking” along the gas pipe. Only when the leakage point(s) has (have) been found and at least provisionally sealed, the fault clearance is completed and any subsequent measures can be undertaken or planned.