Table of Contents
The maintenance of gas systems is of central importance for ensuring operational safety. For this purpose, an extensive set of rules has been created, specifying the exact requirements for the type and extent of maintenance. However, the terms “maintenance” and “gas installation” alone cover a wider range of topics, so we will narrow down and classify the terms below.
Maintenance and gas installation
Maintenance refers to DIN 31051 and includes maintenance, inspection and repair.
- Maintenance = measures to maintain the established condition
- Inspection = Action to determine and evaluate the actual condition
- Repair = Action to restore the specified condition
In the current DVGW worksheet G 495, the term “maintenance” also includes the functional test. This refers to testing the function of a gas installation directly on site. According to the worksheet, the functional test always includes an inspection. Both together are summarised there under the term “maintenance”. Ultimately, it is a question of determining and assessing the actual condition of a gas installation in order to be able to decide on the basis of these findings whether the target condition is to be maintained. The functional test is carried out at least by a person who has undergone special training, and in some cases also by a professional expert.
According to DVGW G 495, a gas installation is the combination or connection of components and assemblies to form a structurally or functionally delimited system. Examples include complete gas pressure regulating stations as well as gas pressure regulators, in particular house pressure regulators according to DVGW G 459-2 and G 600 (TRGI 2018).
Predetermined vs. condition-based maintenance
In worksheet G 495, maintenance for gas systems is also divided into two types. In the case of predetermined maintenance, this is carried out according to fixed deadlines, which are to be understood as maximum deadlines and may not be exceeded. For the actual periods, which may be shorter and may even have to be shorter, the operating conditions, operational requirements and experience must be taken into account.
Condition-based maintenance was introduced with the publication of the previous edition of Code of Practice G 495 in July 2006. These code was introduced due to the requirement that maintenance should be considered from an economic point of view in addition to the aspect of operational safety, and the regulations has been continuously developed since then. Here, maintenance is largely carried out as required. The basis for the implementation of condition-based maintenance is the introduction of an evaluation system that must be based on user-understandable criteria. The demands on the personnel are higher for this, as is the effort, e.g. for documenting the condition of the system. However, condition-based maintenance offers the possibility in the medium to long term to further exploit existing utilisation potentials in the area of maintenance.
In practice, the already established predetermined maintenance is used in many places, but condition-based maintenance is becoming increasingly important due to its economic attractiveness – from a long-term perspective – and due to the experience now available in the companies. When deciding on one of the two types of maintenance, the recommendations of the manufacturer of gas pressure regulators should be taken into account in addition to operational requirements and experience.
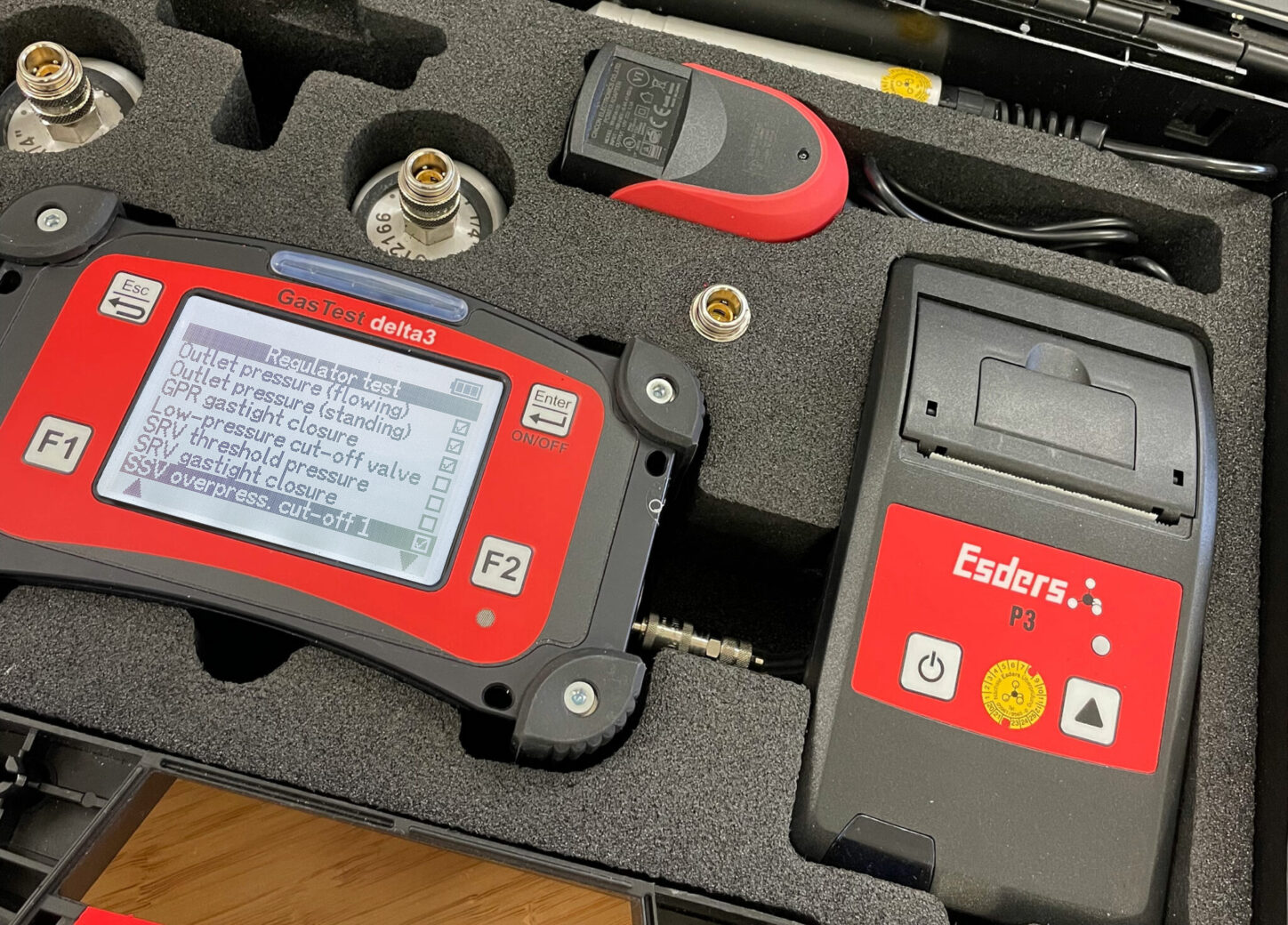
In the following, we will concentrate on the functional test as an essential part of maintenance and take a closer look at gas pressure regulators, especially so-called house pressure regulators. This also includes the so-called meter regulators.
Deadlines
The functional test of a gas pressure regulator is usually carried out on site in the installation without any intervention in the device. When implementing the functional tests, a semi-automated test facility should be used if possible in order to minimise subjective errors and make the results more accurate. The results of the test should be adequately documented.
The periods for testing depend on the maximum inlet pressure as well as the maximum volume flow, i.e. the flow rate. In practice, a distinction is typically made between low-pressure regulators (up to 100 mbar inlet pressure) and medium-pressure regulators (from 100 mbar to 1 bar inlet pressure). Only in the case of medium-pressure regulators is the flow rate also taken into account when determining the deadlines; in the case of low-pressure regulators this is omitted due to the low flow rates. With these regulators, the function test is only carried out as required, i.e. according to operational requirements based on operating experience. Since no safety devices such as a safety shut-off valve (SSV) are installed here, the functional test is usually limited to an output and closing pressure measurement as well as the tight shut-off of the regulator.
In the case of medium pressure regulators, a safety shut-off device is always installed, usually an SSV, due to the increased hazard potential. Consequently, the inspection intervals are also more strictly regulated here. With a maximum flow rate of up to 200 m3/h, a maximum period of twelve years applies after predetermined maintenance period. If the flow exceeds 200 m3/h, the period is reduced to a maximum of four years.
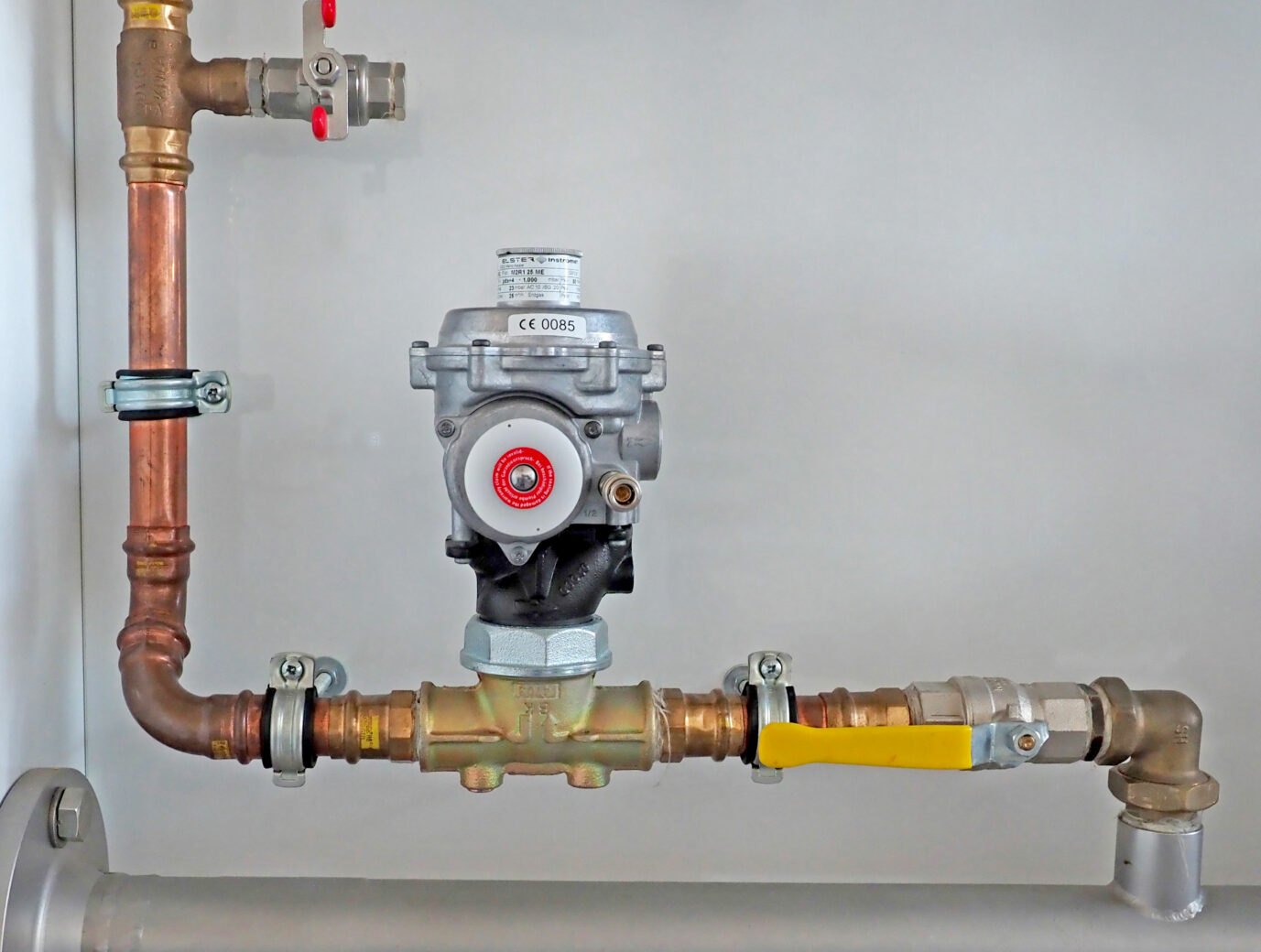
The low-pressure and medium-pressure regulators mentioned above fall within the scope of worksheet G 459-2, whereby reference is made to worksheet G 495 with regard to the inspection intervals. These are mainly used in the private or (small) commercial sector. High-pressure regulators up to a maximum inlet pressure of 5 bar are also still covered by this worksheet. However, these regulators are more likely to be found in the commercial or industrial sector due to the higher gas demand. Compared to low and medium pressure regulators, the maximum inspection intervals for high pressure regulators are halved to six (up to 200 m3/h) or two (over 200 m3/h) years.
The functional test of a gas pressure regulator according to G 459-2 or G 495 is part of the daily work of a network operator. It is therefore an essential part of ensuring the operational safety of gas systems in the domestic, but also in the commercial sector. We discuss how the test is carried out in practice here.